【技术领域】:本发明涉及熔融还原炼铁领域,特别是一种HIsmelt熔融还原炉炉顶煤气处理工艺。
【背景技术】:HIsmelt炼熔融还原铁工艺是一种以非焦煤作为主要能源,直接使用铁矿粉等原料,在高温熔融状态下用碳把铁氧化物还原成金属铁的冶炼方法。该方法不用焦炭、烧结矿和球团矿,大大的减少了CO2、NOx和二恶因的排放,具有工艺简单、资源和能源利用效率高、对环境污染小等优点,具有十分光明的应用前景,一直以来也是炼铁行业研究的热点。相比高炉炼铁,HIsmelt熔融还原工艺产生炉顶煤气在1500~1700℃之间,具有气量大、热值高、温度高等特点,而且在炉顶煤气中还附带有一定的烟尘,因此给HIsmelt炉顶煤气的回收利用带来了极大的难题。
针对HIsmelt熔融还原工艺产生炉顶煤气回收利用存在的问题,本专利的发明内容在于提供一种HIsmelt熔融还原炉炉顶煤气处理工艺,通过该烟气处理工艺,一方面降低炉顶烟气中的粉尘量,将大部分炉尘排出,减轻了煤气洗涤的除尘负担;另一方面,余热锅炉将烟道中不能回收的余热进一步回收,可从烟道出口800℃左右降低至余热锅炉出口的140~150℃,大大提高的余热回收效率,实现了能源的高效回收利用。
【发明内容】:本专利的发明内容在于提供一种HIsmelt熔融还原炉炉顶煤气处理工艺,该方法利用烟道式汽化冷却装置回收SRV炉在冶炼时高温烟气中的余热、降低排烟气温度,然后通过旋风分离器,将烟气中的大颗粒粉尘在旋风除尘器内沉降后进入对流换热锅炉,利用余热锅炉进一步对烟气的预热进行利用。该工艺方法在汽化冷却系统后增加了旋风除尘系统和余热锅炉系统,通过该烟气处理工艺,一方面降低炉顶烟气中的粉尘量,将大部分炉尘排出,大大减轻了煤气洗涤的除尘负担;另一方面,余热锅炉将烟道中不能回收的余热进一步回收,可从烟道出口800℃左右降低至余热锅炉出口的140~150℃,大大提高的余热回收效率,实现了能源的高效回收利用。
【本发明的技术方案】:本专利的发明内容在于提供一种HIsmelt熔融还原炉炉顶煤气处理工艺,该方法利用烟道式汽化冷却装置回收SRV炉在冶炼时高温烟气中的余热、降低排烟气温度,然后通过旋风分离器,将烟气中的大颗粒粉尘在旋风除尘器内沉降后进入对流换热锅炉,利用余热锅炉进一步对烟气的预热进行利用。该处理工艺包括如下步骤:
第一、SRV炉产生的温度为1400~1650 ℃的烟气首先进入烟道式汽化冷却装置,以回收SRV炉在冶炼时高温烟气中的余热、降低排烟气温度;
第二、烟气在汽化烟道内被冷却到750~880℃后,来自汽化冷却烟道的废气首先进入旋风分离器,烟气中的大颗粒粉尘在旋风除尘器内沉降;
第三、经过旋风除尘器后的烟气进入对流换热锅炉,在余热锅炉系统被冷却到210~250℃后进入烟气净化系统;
所述步骤一中汽化冷却烟道采用强制与自然对流循环,给水为除盐水。
所述步骤一中预热回收方式,指来自低压汽包的150℃除氧水,经给水泵送到中压包,循环水经下降管进入烟道各受热面吸热后返回中压汽包,蒸汽送到燃气锅炉去过热。
所述步骤一中汽化冷却装置由汽化冷却烟道、中压汽包、高压强制循环泵、循环管道、压力释放阀等组成。
所述步骤二进入预热锅炉前,先进旋风除尘除去烟气中的大颗粒粉尘,对烟气进行初步的净化。
所述步骤三中余热锅炉为对流换热锅炉,余热锅炉水循环方式为自然循环。
所述步骤三中产生蒸汽通过管网外送发电,系统平均产蒸汽100~140 t/h,工作压力4.0~5.5MPa。
【本发明的优点及效果】:本发明专利涉及一种HIsmelt熔融还原炉炉顶煤气处理工艺,该方法利用烟道式汽化冷却装置回收SRV炉在冶炼时高温烟气中的余热、降低排烟气温度,然后通过旋风分离器,将烟气中的大颗粒粉尘在旋风除尘器内沉降后进入对流换热锅炉,利用余热锅炉进一步对烟气的预热进行利用。所涉及的方案具有以下优点及有益效果:首先,相比于传统HIsmelt熔融还原炉烟气处理工艺,在汽化冷却系统后增加了旋风除尘系统和余热锅炉系统,通过该烟气处理工艺,一方面降低炉顶烟气中的粉尘量,将大部分炉尘排出,大大减轻了煤气洗涤的除尘负担;其次,余热锅炉将烟道中不能回收的余热进一步回收,可从烟道出口800℃左右降低至余热锅炉出口的140~150℃,大大提高的余热回收效率,实现了能源的高效回收利用。同时,该工艺高效可行,具有操作简便、运行可靠等优点。对实现HIsmelt工艺的高效、稳定生产提供了重要支撑技术。
【附图说明】:
图1为HIsmel矿煤混喷管线布置示意图
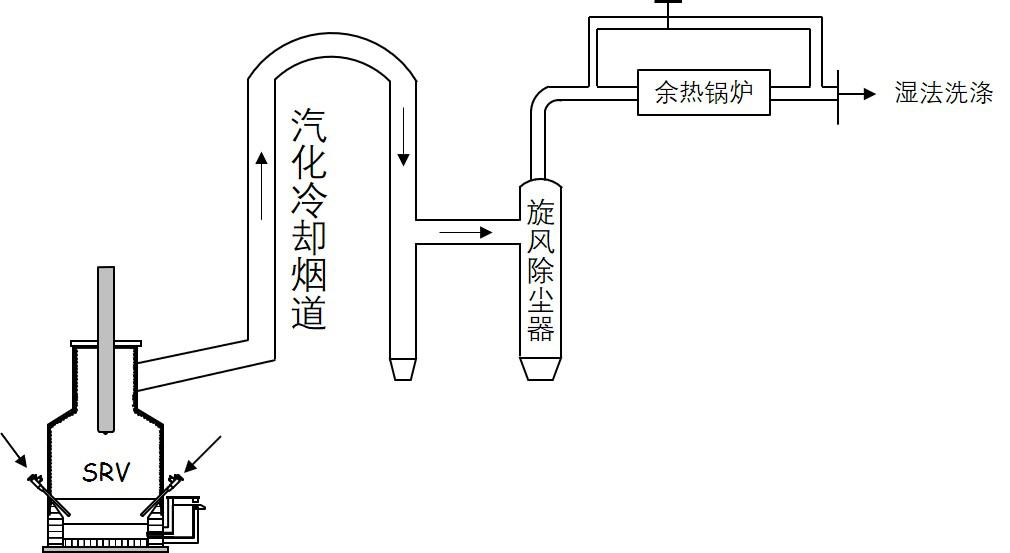
【具体实施方式】:
实施例1:
如图1所示,正产生产过程中,SRV炉产生的温度为1400~1650 ℃的烟气首先进入烟道式汽化冷却装置,以回收SRV炉在冶炼时高温烟气中的余热、降低排烟气温度,汽化冷却烟道采用强制与自然对流循环,给水为除盐水。烟气在汽化烟道内被冷却到750~880℃后,来自汽化冷却烟道的废气首先进入旋风分离器,将烟气中的大颗粒粉尘在旋风除尘器内沉降。经过旋风除尘器后,进入对流换热锅炉后外送发电,系统平均产蒸汽100~140 t/h,工作压力4.0~5.5 MPa,烟气在余热锅炉系统被冷却到210~250℃后进入烟气净化系统。
本发明专利涉及一种HIsmelt熔融还原炉炉顶煤气处理工艺,该方法利用烟道式汽化冷却装置回收SRV炉在冶炼时高温烟气中的余热、降低排烟气温度,然后通过旋风分离器,将烟气中的大颗粒粉尘在旋风除尘器内沉降后进入对流换热锅炉,利用余热锅炉进一步对烟气的预热进行利用。新型烟气处理工艺相比于传统HIsmelt熔融还原炉烟气处理工艺,在汽化冷却系统后增加了旋风除尘系统和余热锅炉系统,通过该烟气处理工艺,一方面降低炉顶烟气中的粉尘量,将大部分炉尘排出,大大减轻了煤气洗涤的除尘负担;其次,余热锅炉将烟道中不能回收的余热进一步回收,可从烟道出口800℃左右降低至余热锅炉出口的140~150℃,大大提高的余热回收效率,实现了能源的高效回收利用。同时,该工艺高效可行,具有操作简便、运行可靠等优点。对实现HIsmelt工艺的高效、稳定生产提供了重要支撑技术。
1、本专利的发明内容在于提供一种HIsmelt熔融还原炉炉顶煤气处理工艺,该方法利用烟道式汽化冷却装置回收SRV炉在冶炼时高温烟气中的余热、降低排烟气温度,然后通过旋风分离器,将烟气中的大颗粒粉尘在旋风除尘器内沉降后进入对流换热锅炉,利用余热锅炉进一步对烟气的预热进行利用。该处理工艺包括如下步骤:
第一、SRV炉产生的温度为1400~1650 ℃的烟气首先进入烟道式汽化冷却装置,以回收SRV炉在冶炼时高温烟气中的余热、降低排烟气温度;
第二、烟气在汽化烟道内被冷却到750~880℃后,来自汽化冷却烟道的废气首先进入旋风分离器,烟气中的大颗粒粉尘在旋风除尘器内沉降;
第三、经过旋风除尘器后的烟气进入对流换热锅炉,在余热锅炉系统被冷却到210~250℃后进入烟气净化系统;
2、根据权利要求1所述步骤一中汽化冷却烟道采用强制与自然对流循环,给水为除盐水。
3、根据权利要求1所述步骤一中预热回收方式,指来自低压汽包的150℃除氧水,经给水泵送到中压包,循环水经下降管进入烟道各受热面吸热后返回中压汽包,蒸汽送到燃气锅炉去过热。
4、根据权利要求1所述步骤一中汽化冷却装置由汽化冷却烟道、中压汽包、高压强制循环泵、循环管道、压力释放阀等组成。
5、根据权利要求1所述步骤二进入预热锅炉前,先进旋风除尘除去烟气中的大颗粒粉尘,对烟气进行初步的净化。
6、根据权利要求1所述步骤三中余热锅炉为对流换热锅炉,余热锅炉水循环方式为自然循环。
7、根据权利要求1所述步骤三中产生蒸汽通过管网外送发电,系统平均产蒸汽100~140 t/h,工作压力4.0~5.5MPa。