摘要:分析了世界及中国直接还原铁的技术现状。直接还原工艺可以摆脱焦煤资源短缺的束缚,降低 CO2排放,促进资源综合利用,且高品质的直接还原铁是生产洁净钢不可缺少的原材料,是钢铁工业发展不可缺少的组成部分。随着铁矿精选技术、煤制气技术的成熟,从及气基竖炉生产规模的不断增大,煤制气 →竖炉将成为中国主要的直接还原生产工艺。高温高料层 PSH工艺应当具有良好的应用前景。回转窑、隧道窑等工艺在特定地区可适当发展,但不会成为直接还原铁生产的主流。
关键词:直接还原;气基竖炉; PSH工艺;竖炉
文献标志码: A文章编号: 0449-749X(2017)01-0007-06
钢铁工业是国民经济生产中CO2排放量最大的行业之一。传统的高炉→转炉工艺,吨粗钢CO2排放量超过2.15 t。减少CO2排放,实施绿色发展是钢铁工业生存和发展的重要课题[1]。随着钢铁存量及废钢回收量的增加,废钢→电炉炼钢的产量持续增长。经济发达国家电炉钢产量占粗钢的产量已超过50%。中国的钢铁产量中,90%是采用传统的高炉→转炉流程生产的,对环境的负面影响大,CO2排放量大。扣除中国,世界钢铁工业的铁钢比为0.70,工业化发达国家的铁钢比仅为0.50,而2015 年中国钢铁工业的铁钢比为0.84[2],这是中国粗钢能耗远高于世界平均能耗的主要原因,使中国钢铁工业成为环境负面影响最大的工业之一,制约了中国钢铁工业的发展。
传统钢铁流程中,高炉炼铁不仅将矿石中铁的氧化物还原为金属铁,同时将矿石中硫、磷、硅、锰、钛、钒等的氧化物部分还原,并进入铁水,增加了炼钢工艺的负担。(1)高炉炼铁是一个脱氧增碳的过程,铁水中碳成分为饱和;(2)转炉炼钢是一个脱碳增氧的过程,脱除铁水中95%的碳是其主要任务;(3)精炼工艺需要再进行脱氧处理。从能源消耗的角度来看,该生产路线不是十分合理,这是传统高炉→转炉工艺无法进一步降低能耗和CO2排放量较高的重要原因。而直接还原铁中碳质量分数通常小于1.50%,且含有一定铁氧化物,可直接与还原铁内的碳反应,仅炼钢工序的吨钢CO2排放量即可降低120~160 kg。因此,发展直接还原可减少钢铁冶炼对环境的负面影响,是绿色发展的方向之一。
铁矿石或铁精矿通过直接还原可生产高品位直接还原铁,显著降低钢水中残留元素,有利于推动和促进洁净钢、优质钢生产的发展和钢铁产品结构的改善。直接还原法可有效阻止其他元素进入金属相,是提高钢铁产品质量有效手段之一。炼焦生产是钢铁生产中对环境负面影响较大环节之一,采用非高炉炼铁技术可以摆脱焦煤资源的束缚,改善钢铁生产的能源结构。因此,摆脱焦炭资源的束缚是直接还原炼铁工艺发展的动力之一。直接还原工艺可有效地实现资源综合利用[4-5],这也是直接还原技术发展的动力之一。
1世界直接还原铁生产概况
近年来,全球直接还原铁产量持续增加(图 1)[2]。 2014年全球直接还原铁产量为 7455万 t,2015年为 7257万 t。近两年,美国、巴林等国家、地区的直接还原铁产量增长明显。
表 1所示为世界范围内各种直接还原铁工艺的产量 [6]。气基竖炉是直接还原铁生产工艺中比较成熟、单机产能较大(最高可达 250万 t/a)的工艺,是业内公认的占据主导地位的直接还原工艺。由表 1可见,近年来,气基竖炉的产量约可达到世界直接还原铁总产量的 80%。2015年世界直接还原铁的总产量为 7257万 t,气基竖炉产量占 79.8%,煤基仅占约 20%。
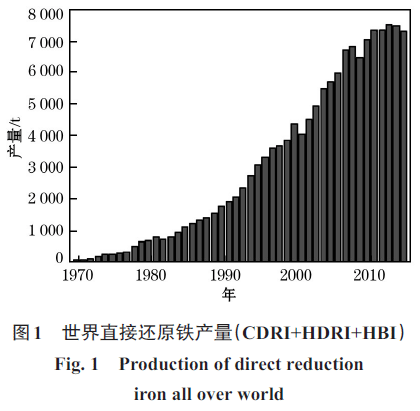
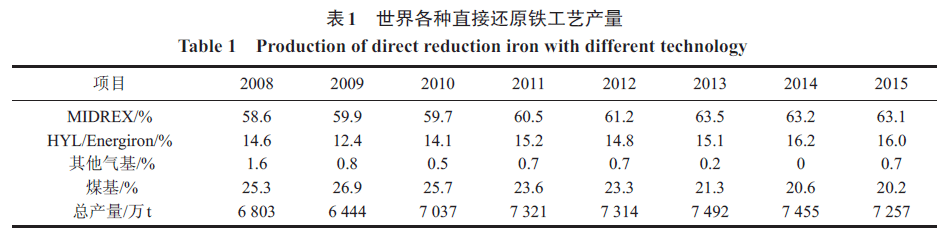
2中国直接还原铁技术的发展状况
2.1直接还原铁生产概况
中国是世界钢铁生产第一大国,粗钢产量已超过 10亿 t,2015年粗钢产量为 8.04亿 t,约占世界总产量的 50%。图 2和图 3分别为近年来“世界和中国 DRI产量及中国占比”和“世界和中国煤基 DRI产量及中国占比”。由图可见,直接还原铁产量与中国粗钢产量第一大国的地位极不相称。中国DRI年产量从未超过60 万t,不仅炼钢用DRI 产量不足世界总产量的1%,单独从煤基DRI产量统计也可看出,最高时的产量也不到世界煤基总产量的7%。DRI的极低产量严重影响了中国洁净钢和优质钢的生产和装备制造业的发展。中国从20 世纪50 年代开始,对直接还原技术进行了广泛的开发和研究。因受资源条件的限制,开发研究主要集中在煤基直接还原工艺(回转窑、隧道窑、转底炉、多种固定床、移动床等),但成效甚微。对于图2 和图3 及中国直接还原铁的生产状况,归纳起来主要有以下几点。

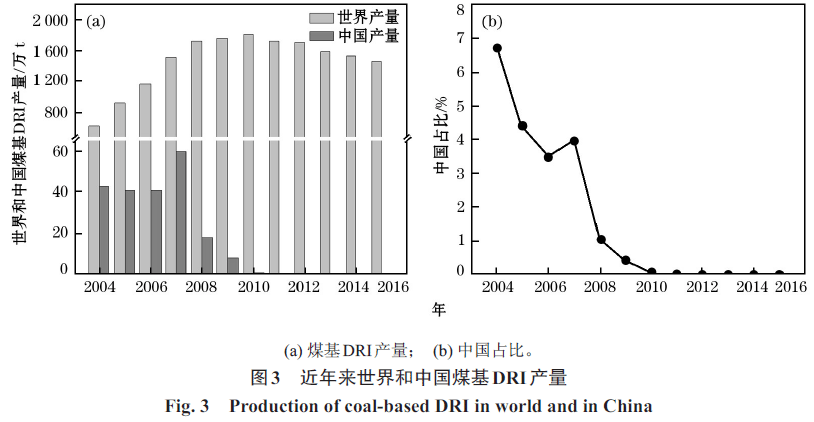
(1)图中数据只计算炼钢用DRI,不包括粉末冶金用的一次还原铁粉。目前,中国粉末冶金用铁粉的产能约为36 万t,分为雾化铁粉和还原铁粉,约各占一半,还原铁粉的产能约为16~17 万t。
(2)中国的直接还原铁主要由回转窑和隧道窑生产,但2008 年以后由于资源的限制,中国DRI 的产量全部是隧道窑产品。
(3)经济分析。近年来,废钢价格持续下跌,使直接还原铁在价格上无法与废钢竞争。因此,导致中国2010年以来直接还原铁产量接近为零。
(4)产品指标分析。中国铁精矿粉按品位w(TFe) 为66% 、w(Fe3O4) 为91%、w(SiO2) 为8%计算,即使金属化率达到100%,DRI 产品的品位也只能达到w(TFe) 为89%。因此,中国DRI 产品中约40%的质量达不到国家标准(w(TFe) 大于90%,体密度大于2.0 kg/cm3)。
2. 2 竖炉与PSH工艺状况
本文对中国的竖炉与PSH 直接还原工艺的发展状况进行简要介绍。
2. 2. 1 煤制气→竖炉工艺
近年来,中国钢铁和化工工作者对煤制气、竖炉直接还原进行了大量调查和研究工作。70 年代后期,在韶关钢铁厂建成以水煤气为还原气的气基竖炉工业化试验生产线,进行了长达3 年的试生产。后因缺乏高品位铁矿石、水煤气制气单机生产能力过小等原因未实现工业化生产。80 年代,宝钢开展了BL法煤制气→竖炉生产直接还原铁的半工业化试验研究。试验是成功的,但因含铁原料及制气成本问题未能进行进一步开发。自2005 年开始,中国多家企业设计建设30~100 万t/a 的煤制气→竖炉直接还原铁生产线,但均因种种原因而未能实现工业化。因此,该工艺的工业化应用还有待进一步深入研究和探讨,期待尽快建成一条示范性生产线来推动该工艺的发展。
2. 2. 2 PSH工艺
针对转底炉工艺等含碳球团矮料层操作存在的不足,20 世纪末期,卢维高教授提出了高温高料层操作的“对行直底炉”工艺(paired straight hearth或PSH)[7-8],其工艺原理如图4 所示。高温高料层碳热还原工艺的操作特点即“高温”和“高料层”。该工艺具有高金属化率、高生产效率、高能源利用率、高DRI强度和密度的“四高”特点。
该工艺自从在加拿大McMaster 大学开发以来,得到了欧美国家的高度重视。美国钢铁协会AISI(American Iron and Steel Institute)、美钢联(USSteel)、阿赛洛-米塔尔(ArcelorMittal USA)、中国台
湾中钢公司(CSC)等都投入了大量资金进行实验室试验及半工业化研究。其中,美钢联建立了连续式的对行直底炉设备,中国台湾中钢建立了单料批的高料层碳热还原燃气炉等,但后续工作暂时均没有公开报道。中国的东北大学与唐山奥特斯科技有限公司对该工艺进行过相应的技术攻关研究工作。目前,该工艺的技术优势均已在实验室得到验证,可概括如下。
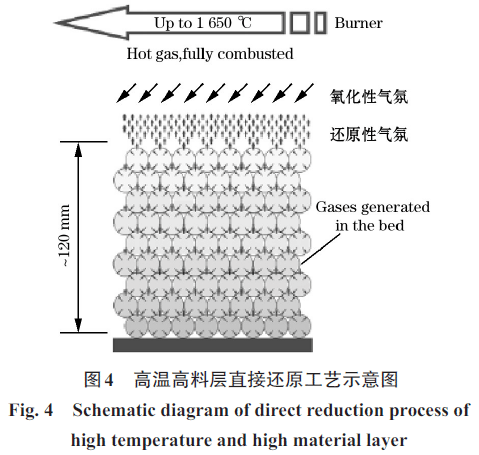
(1)辐射传热。还原初期热量的传递方式是辐射传热,第一层球团经还原体积收缩后,料层空隙度增大,有利于对第二层球团的辐射传热。还原后期底层球团所需热量来自辐射和传导传热的共同作用,此时上层球团的良好还原和收缩使金属化球团DRI 具有优良的导热性能。因此,球团良好的还原和收缩使得整个球团料层具有较大的空隙率(图5),是解决热量传输这一限制性环节的关键,可以保障热量以辐射传热的方式自上而下的传递,解决了由上至下一维辐射传热的限制性环节问题。另外,由于辐射传热量与温度的四次方呈正比,PSH
工艺的高温操作,显著强化了辐射传热量。各料层在还原过程中的温度变化如图6所示。可见底层球团在还原后期也可达到1200℃。
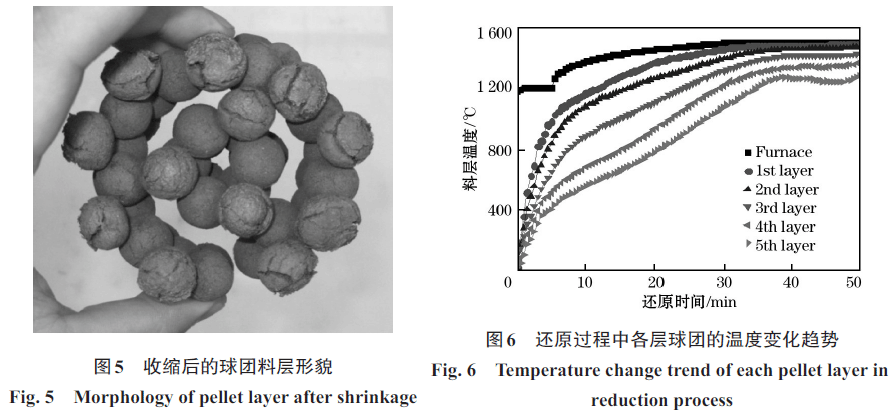
(2)金属化率。高料层碳热还原的金属化率如图7 所示。由图7 可见,炉内还原50 min,各料层球团的金属化率都比较高,5 层料中的上面3 层金属化率约90%以上,下面两层(第4、第5 层)也可达到约78%,整个料层总的金属化率达85%以上。而且,整个还原过程中,金属铁的生成时间越早,生成量越多,越有利于铁晶粒的聚集长大,从而促进DRI 的收缩,密度增大,有利于DRI 的存储和运输。
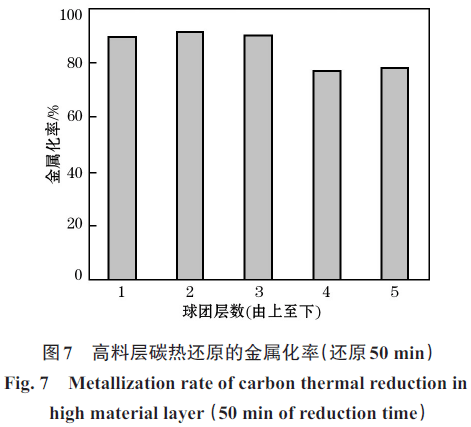
(3)金属铁生产效率。传统的DRI 生产效率单位为kg/ (m2·h),即单位时间、单位面积的DRI 生产量。该指标只考虑了DRI 的产量,没有考虑DRI 的质量。倘若还原时间很短,球团失重就很小,此时DRI 生产效率值很大。即,产量大,但质量差,没有实际意义[9-10]。本文定义单位时间、单位面积的金属铁生产量为金属铁的生产效率,并用金属公式见式(1),单位为kg/ (m2·h)。
金属铁生产效率=DRI生产效率×(w(MFe)/w(DRI)) (1)
式中右边的第一项考虑了DRI 的产量,第二项考虑了w(DRI) (即DRI中w(MFe))。
因为生产的目的是生产金属铁,所以同时考虑产品质量与产量的金属铁的生产效率指标更具有实际意义。料层高度一定时(80 mm),球团尺寸对金属铁生产效率的影响示于图8。可见,对于20~22 mm的球团,还原时间为45、50、55 min 时,生产效率分别为67.20、63.11 和63.43 kg/ (m2·h),远高于单料层操作的生产效率(25~30 kg/ (m2·h))。而且金属化率也比较高,分别为92.28%、93.63%和96.27%。
PSH工艺的技术优势均已在实验室得到验证,其工业化应用的关键在于机械构造和通过高温耐火材料提高其热效率方面。若高温高料层直接还原工艺能够顺利实施,既可以生产低碳铁水,也可以处理某些特殊矿石和含铁粉尘,其产业化前景良好。
燃气炉试验。燃气炉试验由东北大学和奥特斯公司的科研人员共同参与,共进行了No.1(1 450 ℃,60 min)和No.2(1 500 ℃,50 min)两组试验。其中,No.1 温度较低,时间较长;No.2 温度较高,时间较短。炉内温度制度如图9 所示。其他试验参数为:球团的w(C)/w(O)=0.95 时(按固定碳计算),坩埚热装。由试验结果可见(图10),No.1 的还原效果较好,第1~4 层DRI 金属化率为81.59%,第5 层为88.74%,整个料层总的金属化率约为83%。生产效率为50.62或75.49 kg(MFe)(/ m2·h)。与No.2的试验结果相比较,虽然炉内还原时间缩短了,但高温条件下金属化率较高,还原效果更好。可见,在高料层碳热还原技术中,温度参数比时间参数更重要,高温是高料层碳热还原金属化率高、生产效率高的重要原因之一。
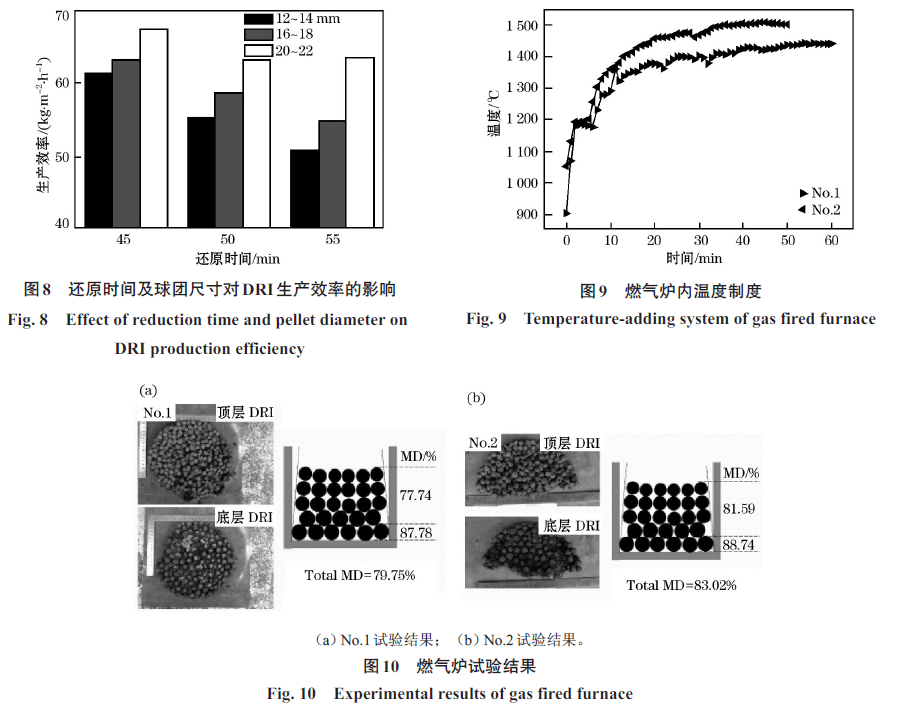
3 展望
(1)直接还原铁市场。中国钢铁工业的发展受到铁矿资源、焦煤资源、废钢资源短缺、环境保护压力的困扰。发展低能耗、环境友好的废钢+DRI→电炉炼钢的钢铁生产短流程是中国钢铁工业的发展方向,中国目前直接还原铁的年需求量约为1 000 万~1 500 万t,高品质的直接还原铁在中国具有广阔的使用前景。
(2)提高直接还原铁质量。中国洁净钢、优质钢生产短缺的是“高品质”直接还原铁。但目前中国生产的直接还原铁因原料含铁较低,产品质量难以满足电炉生产洁净钢、优质钢的要求,除天津钢管回转窑产品w(TFe) 大于94.0%外,多数产品w(TFe) 小于90.00%,且w(SiO2) 高,对电炉炉衬侵蚀严重。隧道窑生产规模较小,产品金属化率、含硫量不稳定,影响电炉生产的稳定性,所以国内生产的直接还原铁不适宜于电炉使用。因此,中国发展直接还原铁生产必须坚持高品质路线,应使直接还原铁产品w(TFe) 大于92.0%,w(S) 小于0.0150%,w(P)小于0.0150%,w(SiO2) 小于3.00%,残留元素低。
(3)关于直接还原工艺的展望。随着选矿技术的发展[10],煤制气→气基竖炉直接还原技术应该是中国发展直接还原铁生产的主导方向。新型直接还原PSH 工艺具有金属化率高、生产效率高、能源利用率高、DRI强度和密度高的“四高”特点,既能生产低碳铁水,也能处理某些特殊矿石和含铁废料,具有良好的应用前景,建设一条示范性工业化生产线是该工艺走向商业化的关键所在。
注:引自《炼铁梦想家》,作者 沈峰满,姜鑫,高强健,魏国,郑海燕