1钢铁业的NOx排放情况
氮氧化物(NOx)是当今主要的大气污染物之一,钢铁工业烧结工序中伴随燃料的燃烧,产生了大量的NOx。中国是世界上的钢铁生产大国,自1996年以来钢铁产量稳居世界第一位。巨大的钢铁产量消耗了大量能源并造成严重的环境污染,2010年全国钢铁行业NOx排放量为93.10万t,占全年工业NOx总排放量的6.3%。NOx排放量增加,不仅危害人类健康,而且使得我国酸雨污染由硫酸型向硫酸和硝酸复合型转变,硝酸根离子在酸雨中所占的比例从上世纪80年代的1/10逐步上升到近年来的1/3。
钢铁生产中各工序排放的NOx比例如表1所示。从中可以看出,烧结工序排放的NOx占钢铁行业NOx总排放量的50%以上。因此,烧结NOx减排是钢铁行业NOx减排的重中之重。
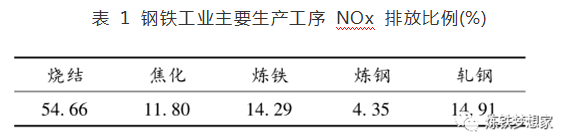
2国内钢铁企业烧结NOx排放水平及控制概况
烧结厂是钢铁生产企业的污染大户,烧结烟气排放的SOx、NOx及粉尘污染最为严重。近几年来,烧结SOx的治理已收到显著成效,NOx的减排也逐渐被提上议程。据有关统计,我国烧结NOx排放浓度一般在200~310mg/m3,最高可达700mg/m3。虽然排放浓度不是很高,但烟气排放总量大,以495m2烧结机为例,其主排气的烟气排放量高达250万m3/h。国内除太钢2台大型烧结机采用了引进日本的活性炭一体化脱硫脱硝脱二恶英烟气净化设备和技术外,尚没有其他烧结机进行烟气脱硝,所以我国烧结NOx减排形势仍然很严峻。为了加大NOx减排力度,国家正逐步提高烧结NOx排放标准,2012年对烧结烟气排放限值作了新的规定,见表2。

3烧结NOx减排控制技术
根据烧结工艺的特点,烧结过程产生的NOx可从三个方面进行控制:原料控制、过程控制(烧结过程脱硝)、末端控制(烧结烟气脱硝)。
3.1烧结原料控制
烧结工序产生的NOx主要为燃料型NOx,90%以上是由烧结燃料(煤粉、焦粉)燃烧产生。因此,控制所用焦粉中氮元素含量及其存在形式,可有效控制NOx排放量。
控制焦粉中氮元素含量最直接有效的方法是选用含氮量较低的焦粉作为烧结燃料,但这增加了选煤的难度。一方面含氮量较低焦粉的供给量远远达不到烧结需求量;另一方面,此类焦粉的价格高于普通焦粉,会增加烧结成本。
NOx的脱除与烧结温度、料层厚度、烧结料粒度及碱度等因素有关。矿石粒度越小,越有利于脱氮反应的进行。料层厚度越高,NOx的生成量越低。此外,提高烧结矿碱度有利于脱氮反应的进行。烧结前,对上层烧结料进行微波加热预处理,也可以降低NOx的排放量。
在烧结原料中加入添加剂以降低NOx生成量,是当今的研究热点之一(铁丝:要考虑副作用)。有研究表明,在烧结料中加入一定量的含钙化合物可降低NOx生成量,添加碳氢化合物(锯末、稻壳、蔗糖等)也可显著抑制NOx生成。YanguangChen等人发明了通过焦粉改性降低烧结NOx排放的新工艺,焦粉中负载的K2O3、CaO和CeO2均能在焦炭燃烧过程中减少燃料氮向NOx的转化,三者效率大小排序为:CeO2>CaO>K2CO3。在烧结杯实验中,以2.0%CeO2和2.0%CaO改性焦粉作固体燃料时,NOx减排率分别为18.8%和13.5%。
3.2烧结过程控制
NOx主要产生于烧结过程,所以对烧结工艺参数加以科学控制能有效降低NOx生成量。控制燃料燃烧过程NOx生成的常用方法有:低NOx燃烧法、低氧燃烧法、分级燃烧法、烟气循环法(FGR)等。由于烧结过程需要保持特定的温度以及氧气浓度,为了保证烧结矿质量,一般不采用低NOx燃烧法、低氧燃烧法和分级燃烧法,而适合采用烟气循环法。烟气循环法是通过收集部分风箱的烧结烟气循环返回至烧结料层,使烟气中的SO2、NOx以及粉尘等污染物被烧结层分解、转化、吸附的工艺。典型的烟气循环技术有EOS工艺、LEEP工艺和Eposint工艺等。
EOS工艺是在烧结机主烟道内抽取40%~45%的烟气与空气混合使氧气含量达到14%~15%,再通入烧结机内作为助燃气体,最终可使烟气排放量降低40%~50%。该工艺不仅利用了烟气中的余热和可燃成份,还降低了NOx、SO2、二恶英等污染物的生成量。1994年荷兰艾默伊登烧结厂在其31号烧结机(132m2)上率先使用了EOS工艺。
根据艾默伊登厂的生产数据,采用EOS工艺后烟气总排放量明显减小,且粉尘、SO2和NOx排放量显著降低,如表3所示。LEEP工艺是根据烧结产生的污染物集中出现在烧结机不同位置而开发的。由于硫氧化物、二恶英等污染物集中产生在烧结机的后半段,所以将该段废气收集起来,经过除尘、与空气混合等一系列处理后再通入烧结机内,从而降低大部分污染物的排放量。烧结机前半段收集的废气污染物浓度较低,故不必循环可直接外排。
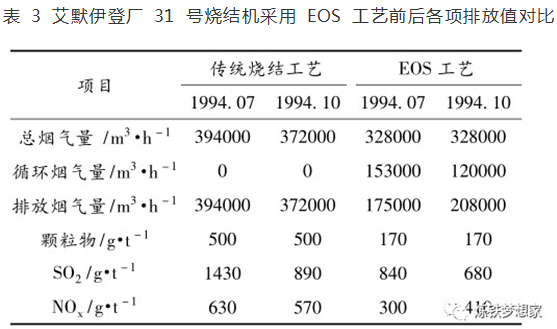
2001年,杜伊斯堡-胡金根厂在420m2烧结机上应用了LEEP技术,结果焦粉消耗降低了5kg/t烧结矿,NOx、SO2和粉尘等主要污染物排放量明显减少,见表4。
表4LEEP工艺应用前后各种污染物排放值对比
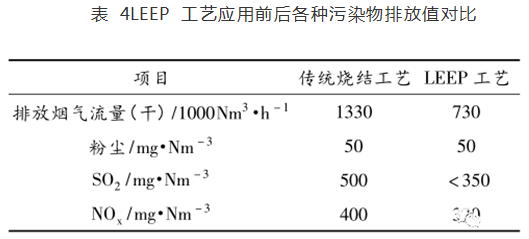
Eposint工艺(EnvironmentalProcessOptimizedSintering)是对EOS工艺的进一步优化。根据Eposint工艺改装后的烧结床,其每个风箱都可单独排出废气。由于烧结料配比及工艺参数会改变,所以烧结机内废气温度升高区域的位置也会发生变化,Eposint工艺的风箱独立排气构造可以只将废气温度升高区域风箱内的废气用于循环,这使得Eposint工艺可以应对各种工艺参数的波动。表5列出了某钢铁厂应用Eposint工艺后的生产数据。从中可以看出,Eposint工艺对NOx、SO2和粉尘等污染物减排效果显著,虽然NOx浓度没有明显变化,但其总量减排效果明显。
表5应用Eposint工艺前后生产数据对比
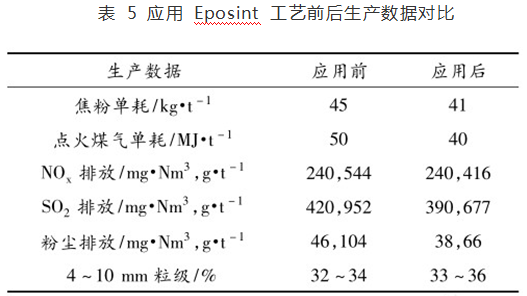
综上所述,三种工艺的基本原理都是利用循环烟气重新进入烧结层,使包括NOx在内的多种污染物在高温条件下被吸附、分解或者转化,从而使排放量降低。在脱硝工程中,应根据企业的实际情况(如:烧结原料结构、设备运转、资金投入、减排目标等),经过论证后,再决定采用何种工艺。
3.3烧结末端控制
当烧结原料含氮量过高或前、中端治理未能达标时,对烧结烟气的处理就显得尤为重要,这是确保NOx达标排放的最终保障。目前,世界上脱硝工程使用的主要工艺有选择性非催化还原法(SNCR)和选择性催化还原法(SCR)。
SNCR工艺是在900~1100℃高温下,还原剂(一般为尿素或氨水)热解生成的NH3有选择地将烟气中的NOx还原为N2和H2O的工艺方法。由于烧结烟气汇合后的温度在200℃以下,使用SNCR技术需要将烟气加热到700℃左右,这在实际生产中是行不通的。
SCR法的原理与SNCR相似,主要差别在于SCR使用催化剂降低了反应活化能,使得反应能在相对较低的温度下(200~450℃)进行。但烧结烟气中的SO2与还原剂NH3反应,生成的(NH4)2SO4及NH4HSO4沉积在催化剂表面,易导致催化剂失活。对烧结烟气先行脱硫可以解决SCR催化剂中毒问题,但会增加投资成本及设备占地面积。
综上所述,烟气脱硝工程中常用SNCR、SCR工艺无法直接应用于烧结烟气脱硝,必须研发新型烟气脱硝技术,以满足日益严格的烧结NOx排放要求。
烧结产生的NOx中,NO占90%以上。NO不易溶于水,与常见的吸收剂无法反应。而NO2在水中具有较大的溶解度,且溶于水后易与吸收剂(如CaO、NH3等)反应。因此,可将NO氧化为NO2后,再进行脱硝处理。UV/H2O2高级氧化工艺是利用UV灯激发H2O2产生的·OH将NO氧化成NO2。其优点是无二次污染,成本低廉,近年来受到了广泛关注,并逐步被应用于脱硝工程中。
单一的脱硫或脱硝成本太高,脱硫脱硝一体化工艺可以达到同时脱硫脱硝的效果,主要工艺有电子束照射法(EBA)、脉冲电晕等离子法(PPCP)、活性炭法(AC)等。
电子束照射法和脉冲电晕等离子法都是通过设备发出的电子束照射烟气,产生的强氧化基团将NOx与SO2快速氧化,氧化生成的NO2、SO3与加入的氨反应最终生成易处理的(NH4)2SO4和NH4NO3。两种工艺的脱硫脱氮效率均可达到80%以上,且对烟气量的变化具有较强的适应性,脱除产物可进一步处理作为肥料使用。但它们都存在能耗高、氨泄漏及运行维护复杂等一系列问题,仍需进一步研究加以解决。
活性炭法(AC)脱硝是在活性炭作用下,烟气中的NOx与加入的NH3发生如下脱硝反应:
2NO+C→N2+CO2
2NO2+2C→N2+2CO2
2NH3+1.5O2→N2+3H2O
4NO+4NH3+O2→4N2+6H2O
烟气中的SO2在活性炭的催化作用下被氧化成SO3,再与水蒸气反应生成H2SO4,被吸附于活性炭之中;活性炭经过加热解吸回收硫酸后可以循环使用。该工艺具有无二次污染,产物可回收利用的优点,最终脱硫率可达90%左右,脱氮率60%左右,但目前合适的活性炭种类还不多,一次脱硫脱硝的效率也不高,需多次进行。但其面临的最大问题在于设备投资及运行成本过高,制约了该工艺在工业脱硝工程中的大规模应用。
烟气综合处理工艺对于烟气中的硫氧化物、氮氧化物、二恶英等多种污染物具有较好的脱除效果,并且具有投资低、占地面积小、技术经济指标优异、运行稳定等优点,因此逐渐受到国家与企业的重视。当前烟气综合处理工艺有NID、MEROS、CFB等。
4结语
烧结是钢铁生产的主要工序,也是钢铁行业NOx排放的主要来源。烧结烟气中除了含有NOx还含有二恶英、SO2等污染物,如果只针对NOx进行单一减排,不仅投资大,能耗高,效果也不理想。因此,采取综合性的烧结污染物减排技术是实现烧结NOx减排的最佳途径。烧结NOx控制应本着“烧结原料控制是基础,烧结过程控制是手段,烧结烟气脱硝是保障”的原则,
从以下几方面着手:
(1)对烧结所用的煤粉和铁矿石进行优选,在资金预算范围内,优先选择含氮量较低的煤粉与铁矿石,从源头上控制烧结NOx的生成。
(2)开发出成本低、效率高、适用于大规模烧结生产的烧结原料添加剂,进一步在烧结源头控制NOx的生成量。
(3)在不影响烧结质量的前提下,针对不同的烧结原料,改变烧结工艺参数(如烧结温度、料层厚度、烧结料粒度和碱度等),以消减烧结过程中NOx的生成量。
(4)应从烧结烟气脱硫、脱硝、除尘等方面考虑综合性的烟气末端控制技术,以降低资金投入,缩短烟气处理线,同时达到减排烟气中多种污染物的效果。
(5)国家对烧结NOx的排放要求日趋严格,我们应根据自身实际情况,结合各厂的工艺特点及现状,开发出高效、成本低廉并且符合我国国情的脱硝技术和烧结烟气深度净化成套技术。
注:引自《炼铁梦想家》,作者 苏玉栋、李咸伟、范晓慧