【技术领域】:本发明涉及熔融还原炼铁领域,特别是一种HIsmelt工艺炉渣金属铁回收方法。
【背景技术】:
HIsmelt工艺历时20多年的发展与研究,已成为世界上最具有工业应用前景的非高炉炼铁新工艺之一。HIsmelt熔融还原工艺可不适用焦炭,而直接使用粉矿和 粉煤,改工艺具有设计简单、投资低、环境友好、产品质量高等优点,同时可处理高磷矿、钒钛矿和工业尘泥,因而发展前景十分光明。2017年8月24日,山东墨 龙与力拓集团正式签约,以向墨龙转让HIsmelt技术的所有知识产权、专利及商标等,至此欧洲杯·买球app官网官方网站完成了HIsmelt技术的完全消化吸收,并且成功获得了该项技 术的推广权。
由于HIsmelt工艺本身的原因,喷入铁浴熔池中的部分矿粉、煤粉还没有完全进行反应,就随炉渣排出炉外,这部分FeO无法回收,另外由于出渣过程熔池的搅 拌作用使还原反应生产的部分小铁珠也被炉渣夹带出来,如果不对炉渣中的铁进行回收,会造成铁资源极大的浪费。原澳大利亚HIsmelt工艺设计中,对炉渣的处 理方式是直接放干渣,根据原工厂生产数据,在渣中的含铁量达到10%,按照HIsmelt工艺设计产能年产80万吨铁,如果按照吨铁渣量为370kg计算,HIsmelt工艺 每年将产生29万吨熔渣,其中熔渣中会含有2.9万吨的铁。因此,直接放干渣将导致大量的生铁随熔渣一起凝固,不能有效回收,导致大量生铁资源的浪费,而且 大量的熔渣凝固,不利于熔渣资源的二次利用。经实践检验,新设计的熔渣处理系统在实现熔渣粒化的同时,可以实现将渣中的部分生铁回收。但是,在熔渣中 生铁回收时,出现熔渣粘包的问题比较严重,导致渣包清理工作量大、时间长等问题,使得被迫放干渣次数增大,大大影响熔渣的再利用。
针对HIsmelt运行过程渣中带铁等现象,本发明专利提供一种HIsmelt工艺炉渣中金属铁的回收方法,该工艺首先通过水淬粒化将SRV炉产生的炉渣处理为小粒 级的炉渣颗粒,然后经过磁选,将熔渣中的富铁颗粒进行回收。该发明路径解决了渣中夹带铁资源的浪费,极大的减少了铁资源的损失,该工艺相比于现有的渣 罐静止倾翻工艺具有系统运行稳定,解决渣包黏渣等问题,提升了系统的作业率。
【发明内容】:
本专利的发明内容在于提供一种HIsmelt工艺炉渣金属铁回收方法,该工艺首先经过熔渣粒化将HIsmelt炉产生的炉渣处理为小粒级的炉渣颗粒,经粒化的熔渣 颗粒通过脱水后分离后,经过磁选,将熔渣中的富铁颗粒进行回收。该发明提供了一种解决HIsmelt炉炉渣中铁元素含量高、无法回收利用的方法。该技术路径减 少了渣中夹带铁资源的浪费,极大的减少了铁资源的损失,该工艺相比于现有的渣罐静止倾翻工艺具有系统运行稳定,解决渣包黏渣等问题,提升了系统的作业 率。
【本发明的技术方案】:本专利的发明内容在于提供一种HIsmelt工艺炉渣金属铁回收方法,该工艺首先经过熔渣粒化将HIsmelt炉产生的炉渣处理为 小粒级的炉渣颗粒,经粒化的熔渣颗粒通过脱水后分离后,经过磁选,将熔渣中的富铁颗粒进行回收。该处理工艺包括如下步骤:
第一、SRV炉产生的高温熔渣,由渣沟流入粒化装置;
第二、通过熔渣粒化工艺,可以将SRV炉产生的熔渣水淬、粒化形成粒度为0~4mm的熔渣颗粒;
第三、熔渣颗粒经磁选机进行磁选,分离富铁颗粒;
第四、富铁颗粒及熔渣颗粒通过输送带进入脱水器,在脱水器中实现渣水分离,水进入坑池中循环利用。
第五、经筛分后的富铁颗粒可以通过回转窑工艺或者直接喷吹的方法实现含铁物料的回收利用。
所述步骤一中熔渣温度为1350℃~1600℃,渣中含铁为3~10%。
所述步骤二中熔渣的粒化方式,可以是转鼓法粒化,也可以是圆盘法进行粒化,渣粒化后的粒度为0~4 mm。
所述步骤三中经过粒化后的熔渣颗粒,经过磁选机进行磁选分离。
所述步骤三中经过磁选熔渣中80~90%的金属铁颗粒可以被回收。
所述步骤四中经分离后的熔渣和富铁颗粒通过滚筒或者其他形式进行脱水。
所述步骤四中经过脱除的水分进入沉淀池进行沉淀,上层清水可循环利用。
所述步骤五中磁选后的金属颗粒经回转窑预热处理或直接喷吹法进入SRV炉以实现二次资源回收。
【本发明的优点及效果】:
本专利的发明内容在于提供一种HIsmelt工艺炉渣金属铁回收方法,该工艺首先将高温熔渣经过水淬粒化,将HIsmelt炉产生的炉渣处理为0~3 mm的小粒级的炉 渣颗粒,然后对细颗粒炉渣进行磁选回收,然后将经粒化的熔渣颗粒、及铁颗粒进行脱水分离,经过磁选,将熔渣中的富铁颗粒进行回收。所设计的方案具有以 下优点及有益效果:首先,该工艺技术减少了渣中带铁资源的浪费,实现了铁资源的回收,降低了HIsmelt炉的运营成本;其次,该工艺相比于现有的渣罐静止倾 翻工艺具有系统运行稳定,解决渣包黏渣等问题,提升了系统的作业率。同时,该工艺高效可行,具有操作简便、运行可靠等优点。对实现HIsmelt工艺的高效、 稳定生产提供了重要支撑技术。
【附图说明】:
图1为HIsmelt炉渣处理工艺设计图
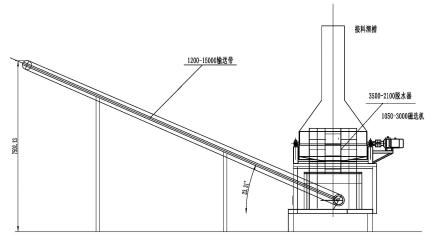
图2为HIsmelt炉渣处理脱水磁选设计图
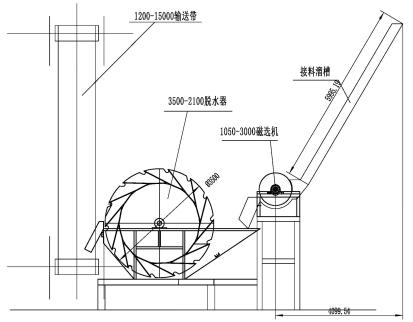
【具体实施方式】:
实施例1:
HIsmelt产生的1500℃左右的炉渣,其中全铁含量约为6%,金属铁含量约为3%,通过高压水淬粒化,可以将SRV炉产生的熔渣水淬、粒化形成粒度为3mm的熔渣 颗粒,经过水淬冷却后,熔渣颗粒被传送带运输至经磁选机进行磁选,分离富铁颗粒,富铁颗粒及熔渣颗粒通过输送带进入脱水器,在脱水器中实现渣水分离, 水进入坑池中循环利用。经筛分后的富铁颗粒可以通过配加入回转窑工艺实现含铁物料的回收利用。
本专利的发明内容在于提供一种HIsmelt工艺炉渣金属铁回收方法,该工艺将高温熔渣经过水淬粒化后形成小粒级的炉渣颗粒,然后对细颗粒炉渣进行磁选回 收。该工艺技术减少了渣中带铁资源的浪费,实现了铁资源的回收,降低了HIsmelt炉的生产成本;同时,该工艺相比于现有的渣罐静止倾翻工艺具有系统运行稳 定,解决渣包黏渣等问题,提升了系统的作业率。同时,该工艺高效可行,具有操作简便、运行可靠等优点。对实现HIsmelt工艺的高效、稳定生产提供了重要支 撑技术。
1.本专利的发明内容在于提供一种HIsmelt工艺炉渣金属铁回收方法,该工艺首先经过熔渣粒化将HIsmelt炉产生的炉渣处理为小粒级的炉渣颗粒,经粒化的熔 渣颗粒通过脱水后分离后,经过磁选,将熔渣中的富铁颗粒进行回收。该处理工艺包括如下步骤:
第一、SRV炉产生的高温熔渣,由渣沟流入粒化装置;
第二、通过熔渣粒化工艺,可以将SRV炉产生的熔渣水淬、粒化形成粒度为0~4mm的熔渣颗粒;
第三、熔渣颗粒经磁选机进行磁选,分离富铁颗粒;
第四、富铁颗粒及熔渣颗粒通过输送带进入脱水器,在脱水器中实现渣水分离,水进入坑池中循环利用。
第五、经筛分后的富铁颗粒可以通过回转窑工艺或者直接喷吹的方法实现含铁物料的回收利用。
所述步骤一中熔渣温度为1350℃~1600℃,渣中含铁为3~10%。
所述步骤二中熔渣的粒化方式,可以是转鼓法粒化,也可以是圆盘法进行粒化,渣粒化后的粒度为0~4 mm。
所述步骤三中经过粒化后的熔渣颗粒,经过磁选机进行磁选分离。
所述步骤三中经过磁选熔渣中80~90%的金属铁颗粒可以被回收。
所述步骤四中经分离后的熔渣和富铁颗粒通过滚筒或者其他形式进行脱水。
所述步骤四中经过脱除的水分进入沉淀池进行沉淀,上层清水可循环利用。
所述步骤五中磁选后的金属颗粒经回转窑预热处理或直接喷吹法进入SRV炉以实现二次资源回收。